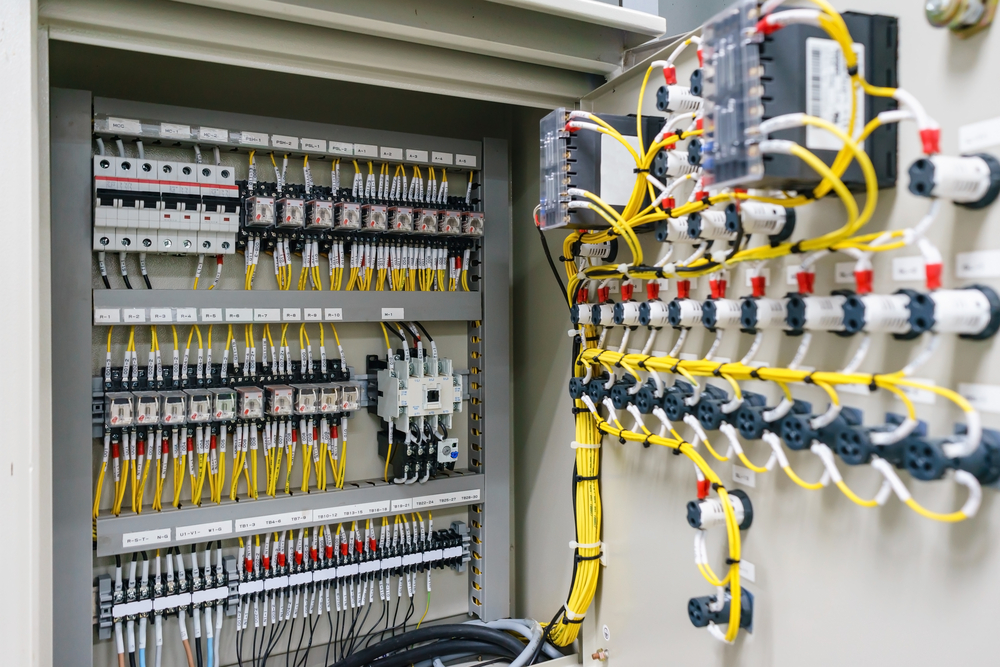
Understanding the Basics of Electrical Contacts
Electrical contacts are foundational to every reliable circuit. Acting as the interface between conductive components, they control the current flow through switching, protection, and signal systems. For engineers and technical buyers, understanding how contacts operate — and what materials perform best — is essential for product reliability and electrical safety.
This article will explore the core concepts behind electrical contacts, break down common types and materials, and examine their applications in modern OEM systems.
What Are Electrical Contacts?
An electrical contact is a conductive interface that allows current to pass between two components. Typically made from silver, copper, or gold, these contacts are engineered to minimize resistance, reduce wear, and maintain high cycle performance under load.
Electrical contacts are integral to devices ranging from power switches and circuit breakers to relays, motor starters, and control panels — especially in industrial and commercial environments.
The Role of Electrical Contacts in Switching Systems
Contacts serve a binary function: to open or close an electrical circuit. They dictate when and how power flows, whether manually operated (as in toggle switches) or electromechanical (as in relays). When contacts "make" (or close), the current flows; when they "brake" (or open), the current flow stops. Their performance is directly tied to safety, uptime, and electrical integrity.
Why Contact Reliability Matters in OEM Applications
For OEMs in sectors such as switchgear manufacturing, automotive electronics, or data center infrastructure, contact failure can lead to:
- Equipment downtime
- Increased heat generation
- Premature component wear
- Safety hazards
- Potential Damage to OEM Brand and Market Position
Material selection, contact surface condition, and contact force design are critical during engineering.
Types of Electrical Contacts
🟩 Fixed vs. Movable Contacts
- Fixed Contacts: Stationary components within a housing or mounting.
- Movable Contacts: Designed to shift position mechanically (manual switches) or electromechanically (relays, contactors).
🟩 Common Contact Materials
Material Applications Strengths
Silver Industrial, switchgear, relays Best conductivity, low contact resistance.
Copper Power electronics, low-cost applications Good conductivity, high thermal transfer
Gold Electronics, sensors Corrosion resistance, low signal loss
🟩 Surface Coatings
Many contacts are plated with the following:
- Nickel: Barrier layer and corrosion protection
- Tin: Cost-effective and solderable
- Silver Compositions (e.g., AgSnO2 - Silver Tin Oxide: Enhanced arc resistance
Applications in OEM Systems
Switchgear & Industrial Controls
Electrical contacts in switchgear assemblies must withstand high fault currents and repeated mechanical cycling. Materials like silver-to-silver and silver-to-copper are standard for critical performance.
Automotive Electronics
Vehicle contacts are exposed to vibration, thermal cycling, and voltage spikes. OEMs use precious metal contacts in ignition, infotainment, and battery management systems.
Heavy Machinery and Robotics
Durable and arc-resistant contacts are critical in relay logic systems, motor control centers, and automation systems to minimize downtime and maintenance cycles.
Best Practices for Contact Maintenance
- Regular Inspection: Look for pitting, discoloration, or wear.
- Cleaning: Use non-corrosive solvents to remove dust and oxidation.
- Timely Replacement: Replace worn contacts with OEM-grade materials to avoid performance degradation.
Conclusion
Electrical contacts may be small, but they perform a big job. In OEM systems — where performance, durability, and safety are non-negotiable — selecting the right contact material and design can define long-term success.
From switchgear to embedded electronics, mastering the fundamentals of contact engineering empowers better sourcing, improved system reliability, and reduced lifecycle costs.
Need Custom Contacts or Busbars for Your Next OEM Project?
Checon supplies engineered electrical contacts, power component assemblies, busbars, and a wide range of custom contact product solutions for high-performance switchgear, power control, and automation systems. Our U.S.-based team partners with OEMs to solve complex current-carrying challenges with custom precision.
🔘 Talk to an Engineer
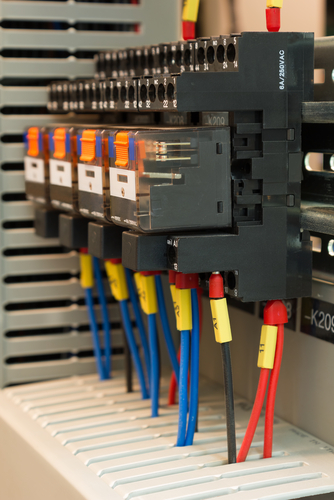
Contact Information
Ed "Mac" McDaries, VP Sales and Business Development, emcdaries@checon.com
Cody Piepenbrink, Sales and Business Development Manager, piepenbrink@checon.com